Incorporated in 2005, Alpha Thermal Process (aka AlphaThermal) is a concept-oriented small business that provides engineering advice and consulting services on the development, design, and selection of process equipment for, and the operation of, high-temperature mineral and materials processing.
Core Competencies
Our core competencies include, but are not limited to, industrial furnaces such as rotary kilns, the ubiquitous industrial workhorse widely used in the related industry, fluidized- and static-bed furnaces. With several new rotary kilns sized in all capacity ranges and several others in operation redesigned and retrofitted for optimized operation, we pride ourselves in being the most knowledgeable in the field with a wide spectrum of process knowhow.
Industries We Serve:
- Minerals, Metals & Materials Processing
- Fuels & Combustion
- Cement & Lime Operations
- Thermal Destruction of Waste
- Lightweight Aggregate
- Power Generation
- Nanoparticle formation and production
- Food Processing, etc.
Pyrotechnical Applications:
- Calcination
- Roasting
- Induration/Sintering
- Simple heating/cooling
- Melting
- Drying
- Ore reduction, extraction, and beneficiation
- Combustion for confined flame applications including industrial furnaces and internal combustion engines.
Our offering approach is twofold including
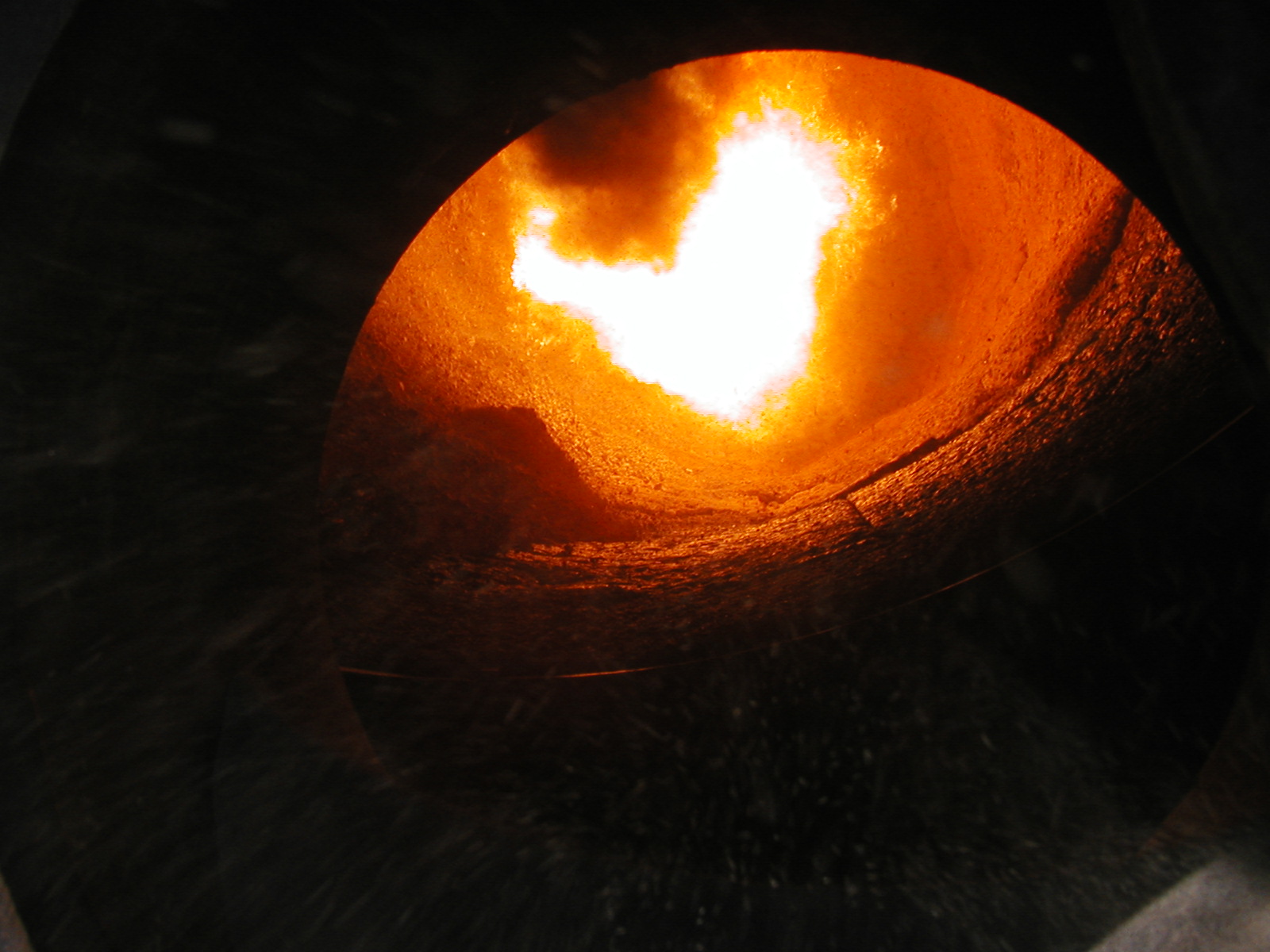